電解研磨(EP)
高い衛生管理や製品組成の安定性に有効な電解研磨
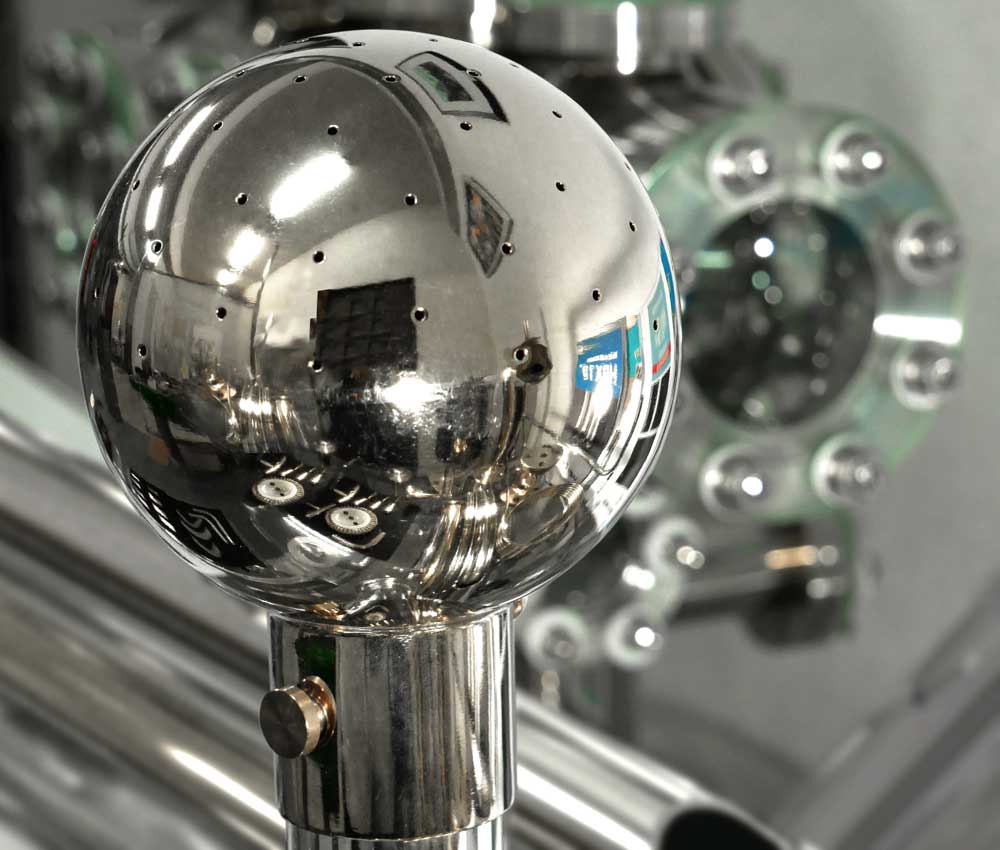
電解研磨(EP)で表面処理された産業用シャワーボール
電解研磨(EP: Electro Polishing, electrolytic polishing, electropolishing)は、ステンレス、チタン、アルミなどの金属表面を電解反応を利用し、極微細な凹凸を溶解し、平滑化・鏡面化された金属面に仕上げる処理です。電解研磨された金属表面には耐腐食性に優れた均質でクロムリッチな不動態皮膜を生成します。
金属表面の汚れ除去 + 汚れを付きにくくする
ステンレス材などをバフ研磨しても、表面には微細なバリ、傷、パーティクルなどが残存します。食品や薬品の生成を行う配管やタンクの場合、滞留物による雑菌の繁殖、製品組成への影響、金属表面の腐食等、品質や安全に関わるトラブルにも繋がりかねません。
(1)研磨剤、金属粉、油脂などの不純物を除去し (2)汚れが付きにくく掃除しやすい平滑面を形成します。
金属表面を均質な皮膜で覆う + 傷ついても被膜が再生しやすい地を作る
様々な問題を起こすサビに対してステンレスは耐腐食性に優れた合金です。しかし、その秘密は金属表面を打合せ不動態皮膜(クロム酸化層)。(3)美しい皮膜を形成し錆に対して隙を作らないこと、そして長期使用に耐えるように、(4)傷がついてもすぐに皮膜を再生し自動修復しやすい下地にすること、が必要です。
電解研磨は、加工しやすく上部でさびにくいステンレスを(1)~(4)でさらに強化。ステンレス配管管やタンク内を常にクリーンな状態にキープします。
目次(リンク付)
1.ステンレスの不動態化皮膜
ステンレスは錆びにくい合金として大変重宝される鉄の合金です。ステンレス(鉄)以外にも、チタンやアルミは化学的には腐食されやすい特性があるものの、その表面に形成される酸化被膜(不動態皮膜)のおかげでサビを寄せ付けない性質があります。またステンレスの不動態皮膜は損傷しても、ステンレス内のクロム(Cr)が外気や水分と結合し、直ちに皮膜を自動修復するので様々な環境でステンレスは利用されています。
電解研磨(EP)は、その名の通り金属表面を電解による溶解によって平滑化も行いますが、むしろ重要なことは、この不動態皮膜を防御と修復に強い完全な状態にすることなのです。

【図1】ステンレスの酸化クロム不動態皮膜
※ステンレスの不動態皮膜は酸化クロム(図左側)だが、実際の環境(大気中など)では、水や酸素と結びつき水和オキシ水酸化物の状態(図右側)の状態で存在する。
サニタリー用のステンレス材であっても、研磨や加工によって金属の表面状態は傷・汚れ・変質などにより、例えば図1の分子モデルのような美しい状態ではありません。「ステンレスは錆びにくい」が額面通りの能力を発揮するためには、ステンレスの表面状態が腐食との戦いに備えた物理的・分子的に整えられた状態である必要があります。電解研磨(EP)は電解処理で、物理的な平滑化と化学的な均質化を行い、ステンレスに最高のコンディションで耐食性を発揮させることができます
2.電解研磨(EP)のメリットと特徴
(1)電解研磨(EP)の特徴
- 処理面が平滑化され鏡面化する
- 緻密な不動態化皮膜が形成される
- 耐食性に優れたクロムが濃縮した層(クロムリッチ層)で覆われる
(2)電解研磨(EP)のメリット
- 汚れを除去する
加工変質層※が除去され耐食性などへの影響が減少する - 汚れを付きにくくする
微粉末や汚れが付着・滞留しにくくなる。それらによる生成製品への影響が現れにくい。
洗浄が容易になりクリーンメンテナンスの負荷が軽減される。 - 錆びにくくする
防錆効果が向上し、腐食による製品への影響や漏出事故が起きにくい。
薬品や食品材料への耐性が向上し、品質を維持しやすい。
(3)なぜ電解研磨(EP)が必要なのか ~ 加工変質層に潜在する問題
加工変質層の問題
加工変質層は、機械研磨等の加工によって金属材質が機械的・熱的に変化した金属の表層を言い、エネルギーが高く化学的に不安定で変化しやすい場所です。また実際には研磨による条痕や傷、研磨剤や有機物内による汚れの付着などで複雑な状態になっています。加工されたステンレス配管などは、このような不安定な層に包まれています。
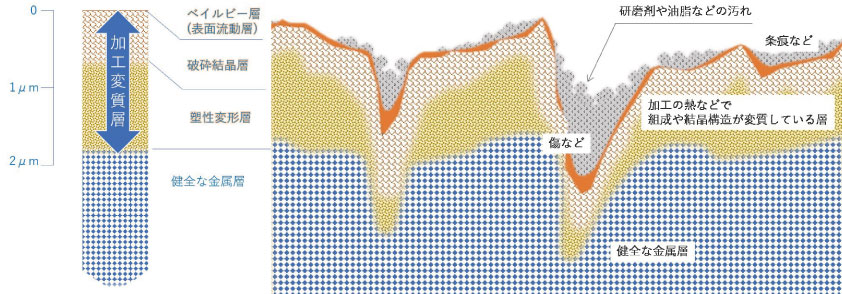
【写真2-3-1】加工変質層と金属表面の潜在的な脆弱性
※図2は金属表面の説明用イメージです。実際の断面写真などを図化したものではなく誇張した想像図です。
ステンレスは金属表面に自然に不働態皮膜を形成することによって耐食性が向上します。しかし表面状態が(ミクロ的に)荒れた状態では、不働態皮膜を大気中で自然形成する場合はもとより、不動体化処理(パッシベーション)で酸化被膜を形成しても、クリーンで均質な不動体膜の形成は困難です。
目視で鏡面に近い状態であっても、将来の腐食の発生や不純物の溶出などトラブルの元凶が内在している可能性があり、シビアな生産環境化では品質問題へとつながる可能性が否めません。
電解研磨(EP)は土壌改良&整地工事
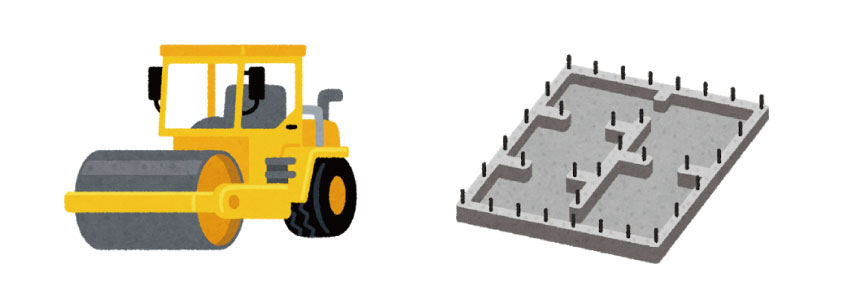
電解研磨処理によって、この不安定な加工変質層を改良し、ステンレスが本来有する特質を最大限に引き出します。それは跡地の再開発のようなものです。
[スクラップなどの撤去]
付着・堆積している汚染物を除去する
[もろい岩を崩し湿地を埋める]
金属の組成・構造的に不安定な部分を溶解
[建機で平坦に整地する]
金属の表面の凹凸を平坦化
[砕石を入れコンクリートを打つ]
整備された金属面上に、均質な不動態膜を形成
これによって、雨水でも土砂が流れず、日照りでもひび割れせず、陥没や隆起も起こらず、掃除もしやすく、通行しやすい安定した土地が生まれるわけです。
ちなみに整地により、土地の測量面積は実際の地表面積の総和とほぼ同じになりますが、金属面でも同様。環境や流動物との接触面積が最小化すればトラブルの可能性も最小化します。
ベイルビー層(Beilby 層):
金属を研磨すると表面に厚さ1~10nm程度の流動性を持ちくぼみを埋め滑面を生じさせる。この層は研磨面のように見えるが、地の金属とは異なる性質を示し、化学的には不安定で変化しやすい状態にある。
塑性変形(そせいへんけい):
かかっていた外力が取り除かれても、その外力による変形が残ったままになる変形のこと。元に戻る変形を弾性変形と呼ぶが、弾性限界を超えると塑性変形となる。
パッシベーション(不動態化処理):
ステンレス鋼は大気中でも酸化被膜を生成するが、薄く不均質なため破壊されやすい。そこで硝酸などの液中に浸漬することで表面を強制的に酸化させ耐食性を強化する処理のこと。汚染物の除去効果もある。
3.電解研磨(EP)の装置構成
電解液中に材料を投入し、金属材料を陽極にして直流通電するものです。
実際の電解研磨は下図モデルのように単純ではなく、材料の形状や電解研磨を施す部位によって電極の形状や配置を調整します。当社は、プレファブ配管や特注容器など複雑な形状や内面への電解研磨のご依頼が多く、様々なノウハウを用いて電解制御を行っています。
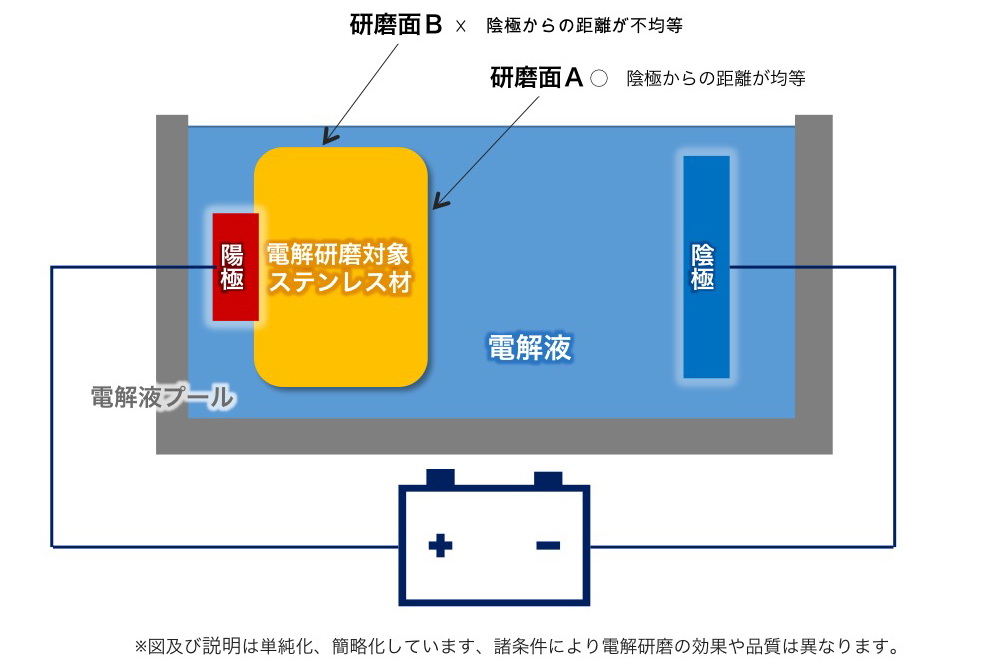
【図3-1】電解研磨装置の構成
※電解研磨はミクロ的な化学反応処理であり、大きな凸凹を除去するものではありません。
※予めステンレス鋼材をバフ研磨などで下処理しておく必要があります。

【写真3-2】ベトナム現地法人 VINA ASTECの電解件研磨装置
4.電解研磨(EP)の原理
サニタリー材(ステンレス)を例にとって電解研磨(EP)の原理をご説明します。
(1)サニタリー材の電解研磨
サニタリー材は、その表面を拡大してみると1/100ミリメートルに満たない程度の研磨痕や傷などが多数あります。また微細なパーティクル等による汚染も存在します。電解研磨によってこれらの凹凸が平滑化される過程を説明します。
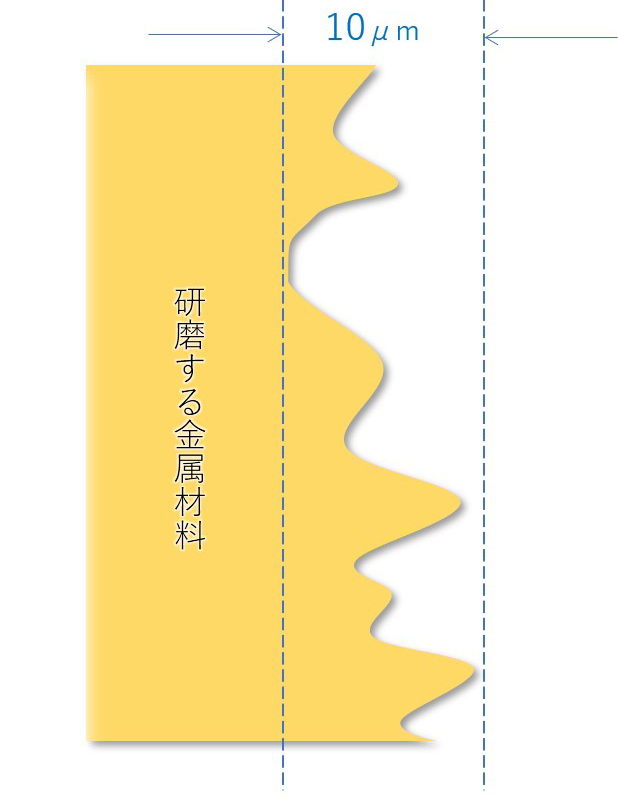
【図4-1】研磨する金属材料の断面イメージ
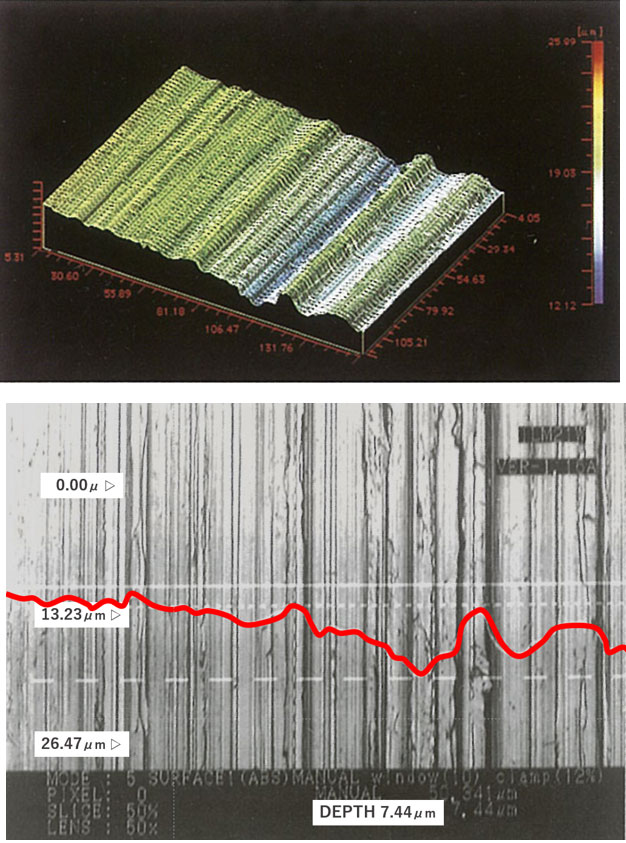
【図4-2】金属材料表面の状況
※単位:1μm(マイクロ・メートル)は10のマイナス6乗メートル。1μm=0.001mm(ミリ・メートル)=1,000nm(ナノ・メートル)
(2)電解研磨液への浸漬
電解研磨するサニタリー材を直流電源の陽極(+)に接続し、電解研磨液に浸漬します。金属材料の電解研磨面(あるいは研磨対象の各面)の全体がおおよそ等しい距離になるよう陰極を設置します。
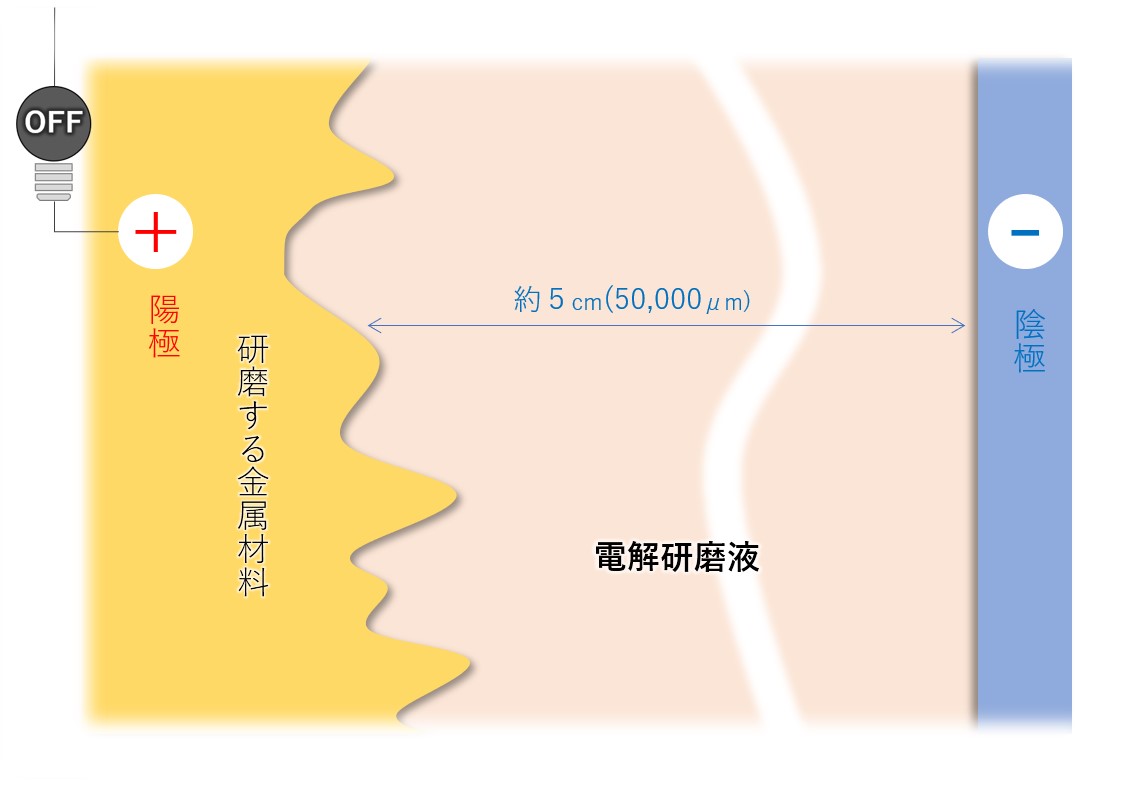
【図4-3】材料を電解研磨液に浸漬する
(3)粘性のある初期酸化層の形成
通電すると、陽極側の金属材料と電解液が反応し、粘性のある初期酸化層が生じます。この層と電解研磨液の境(界面)は概ね平坦になります。陰極を適正に配置すれば界面と電極がほぼ等距離で対峙する形になります。
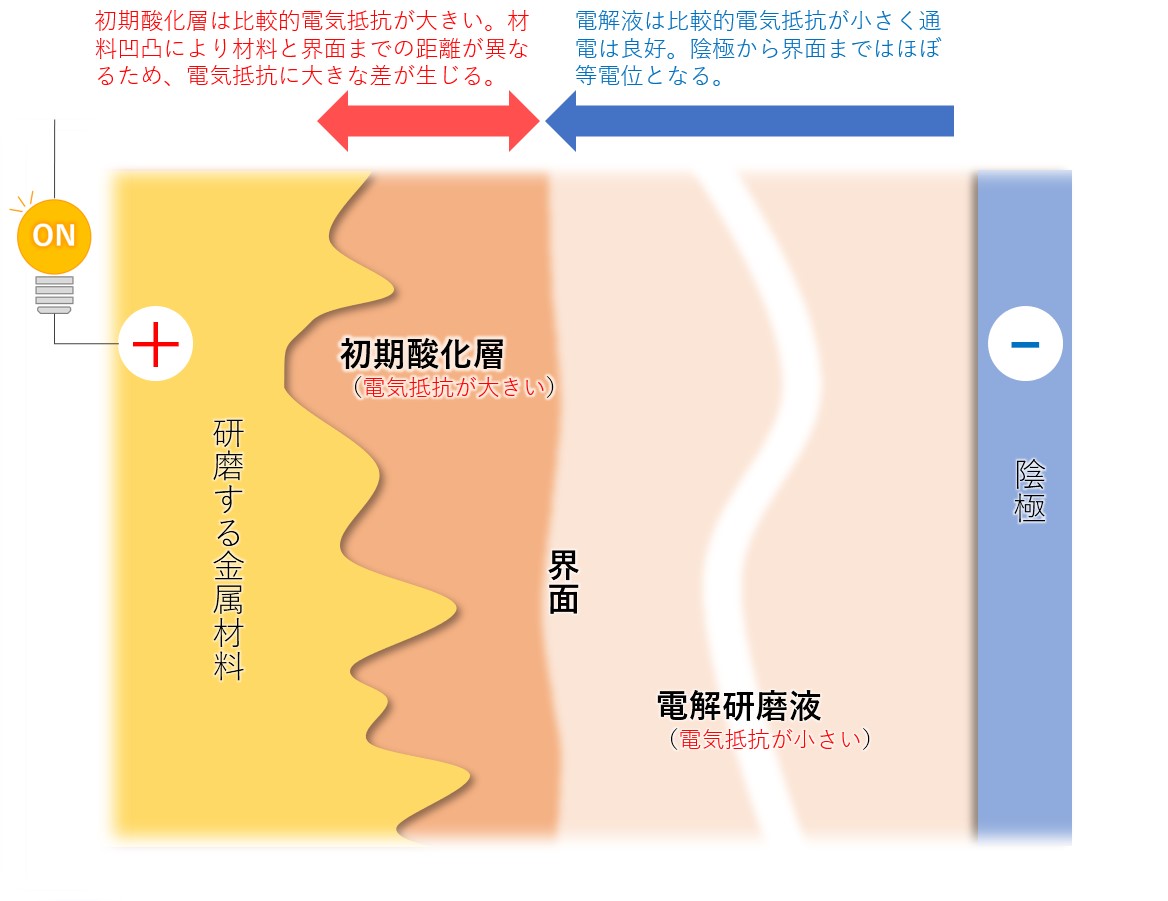
【図4-4】粘性のある初期参加層の形成
通電が良好な電解液に比べ、初期酸化層は電気抵抗が一桁ほど大きく電気が通りにくくなっています。したがって、陰極から界面まではほぼ等電位ですが、そこから金属までは初期酸化層の厚みが電気抵抗となり電流の流れ方に大きな変化が生じます。
(4)金属の凸部から優先的に溶出
界面に向かって突出した金属凸部分は、電気抵抗が少ないので大きな電流が流れ溶解が進みます。金属凹部は界面までの距離があり電流が流れにくいので溶解が起きにくくなります。
したがって、金属の凸部が選択的・優先的に溶解し、金属表面は次第に平坦になっていきます。
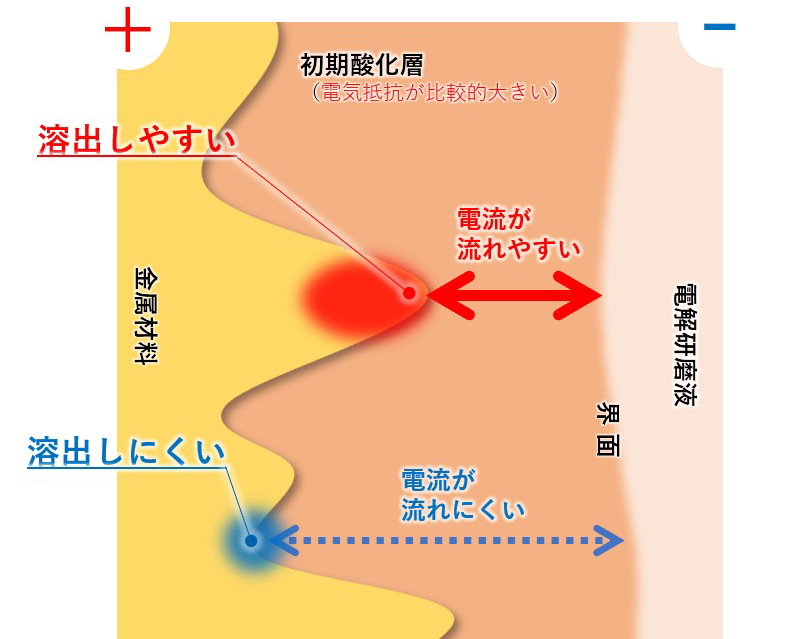
【図4-5】選択的な金属の溶出
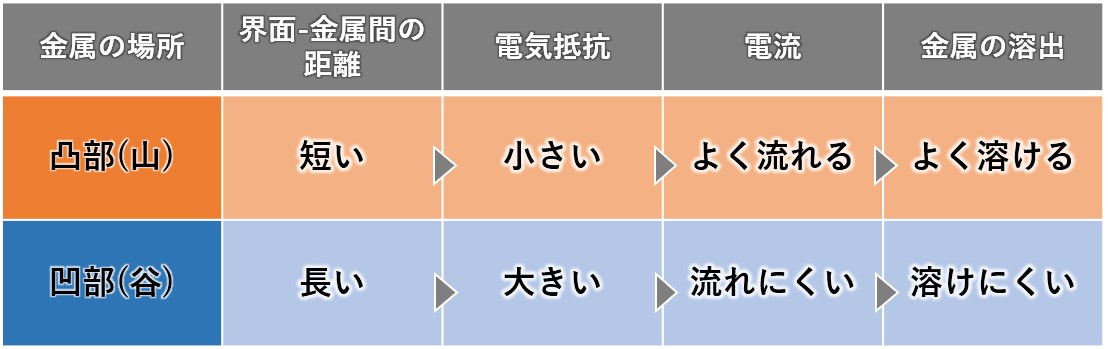
【図4-6】金属表面の凸部が選択的に溶解する理由
(5)電解研磨作用の終息と不動態皮膜の形成
溶解が進みやがて金属面がおおよそ平坦になると、界面と金属の距離が等しくなっていきます。すると金属のどの場所でも電流は一様に流れにくくなるので、電解研磨の作用は次第に小さくなっていきます。
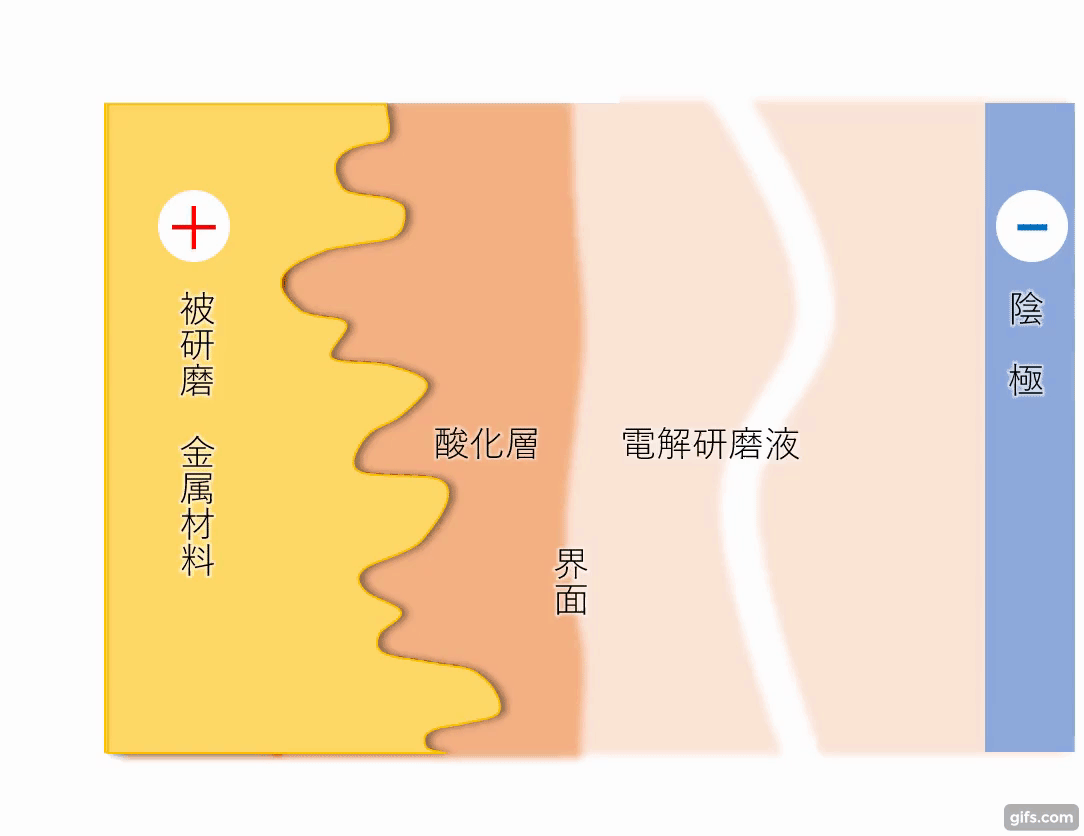
【図4-7】電解研磨が進んだ金属の状態
平坦になった金属面には、極めて均質で強固な不動態皮膜(酸化クロム) が生成され金属表面を覆います。もし一部に皮膜の未形成部分があったとしても、そこに優先的に電流が流れるため、皮膜形成を促進し結果として全体に均質な不動態皮膜が形成されます。
※通常の電解研磨による不動態皮膜の厚みはおおよそ1~3nm(ナノ・メートル)です。
5.電解研磨後の表面付近の状態
ステンレス鋼サニタリー材にバフ研磨を行うと元々形成されていた不動態膜が削り取られるため、通常は硝酸などに漬け強制的に不動態皮膜を形成させます。(硝酸浸漬法・不動態化処理)。しかしこの方法では「ミクロ的には粗い」金属表面上に、均質な不動態皮膜を形成することは困難です。前項で述べたように、電解研磨(EP)であれば汚れも除去され平滑化された良好な金属面上に未形成部分のない均質な不動態皮膜が形成されます。
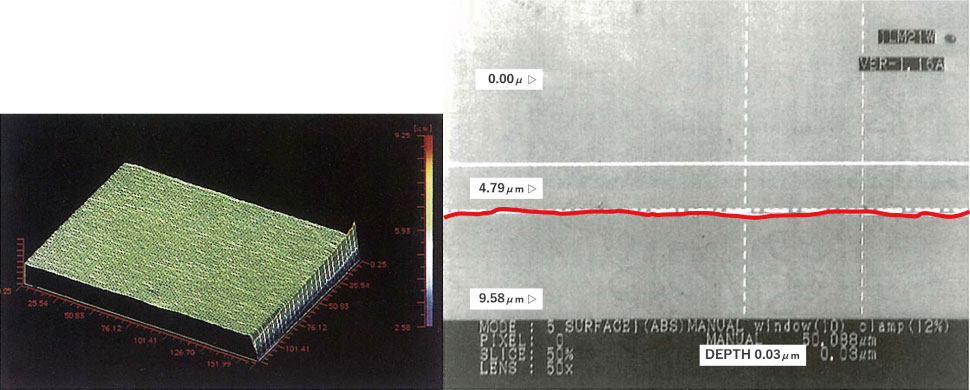
【図5-1】金属材料表面の状況 –電解研磨後
6.より高度な電解研磨 – GOLD EP/ GOLD EP WHITE
当社では、より高い表面品質をお求めのお客様のために、通常の電解研磨(EP)に加え、さらに強固な不動態皮膜を形成するGOLD EP(ゴールドEP/略称GEP)、GOLD EP WHITE(ゴールドEPホワイト/略称GEPW)をご用意しています。
電解研磨処理前 |
電解研磨(EP) |
GEP処理 |
GEPW処理 |
---|---|---|---|
表面は加工変質しており、不均質な酸化状態で、パーティクルも飛び出しやすい。 |
電解研磨によって汚れや不均質な表面が除去され、平坦で滑らかなメタル生地となる。 |
気中雰囲気で熱処理。表面上層には鉄酸化膜、下層にはクロム酸化膜が形成。酸化膜は一般EPの約10倍を持つ2層構造の不動態層となる。 |
上層の鉄酸化膜を薬液で除去。表面は一般EP の約3倍の厚みを持ったクロム酸化膜の不働態層となる。 |
![]() |
![]() |
![]() |
![]() |
表面は、結晶構造の変質や汚れの付着など、物理的な加工の影響を色濃く受けている。 |
耐食性に優れたクロムが濃縮した層(クロムリッチ層) が存在する。厚みは1~3nm(ナノ・メートル) |
残存酸素の多いアルコールやオゾン水などに対し、金属溶出が少ない。 |
超純水、有機アミン系薬液に対し、金属溶出が少ない。 |
【図6-1】一般的な電解研磨(EP)とGOLD EP、GOLD EP WHITEの比較
※GEPはGOLD EPを、GEPWはGOLD EP WHITEを略しています。
GOLD EP/GOLD EP WHITEの特徴
- 金属イオンの溶出や、TOC(総有機炭素)汚染対策に有効
GOLD EP:残存酸素の多いアルコールやオゾン水による溶出に強い
GOLD EP WHITE:超純水や有機アミン系薬液による溶出に強い - 高い平滑度の表面を持ち、パーティクル(塵・ホコリ・異物・ダストなど)に強い
- 耐熱性、耐圧性に優れ適用範囲が広い
- 曲げ加工、フェルール接続、溶接などの加工性や施工性に優れる
- 機械強度はステンレス鋼と同等
- 厚い不動態皮膜の形成による耐食性の強化(GOLD EPの場合、被膜の厚みは一般EP比約10倍)
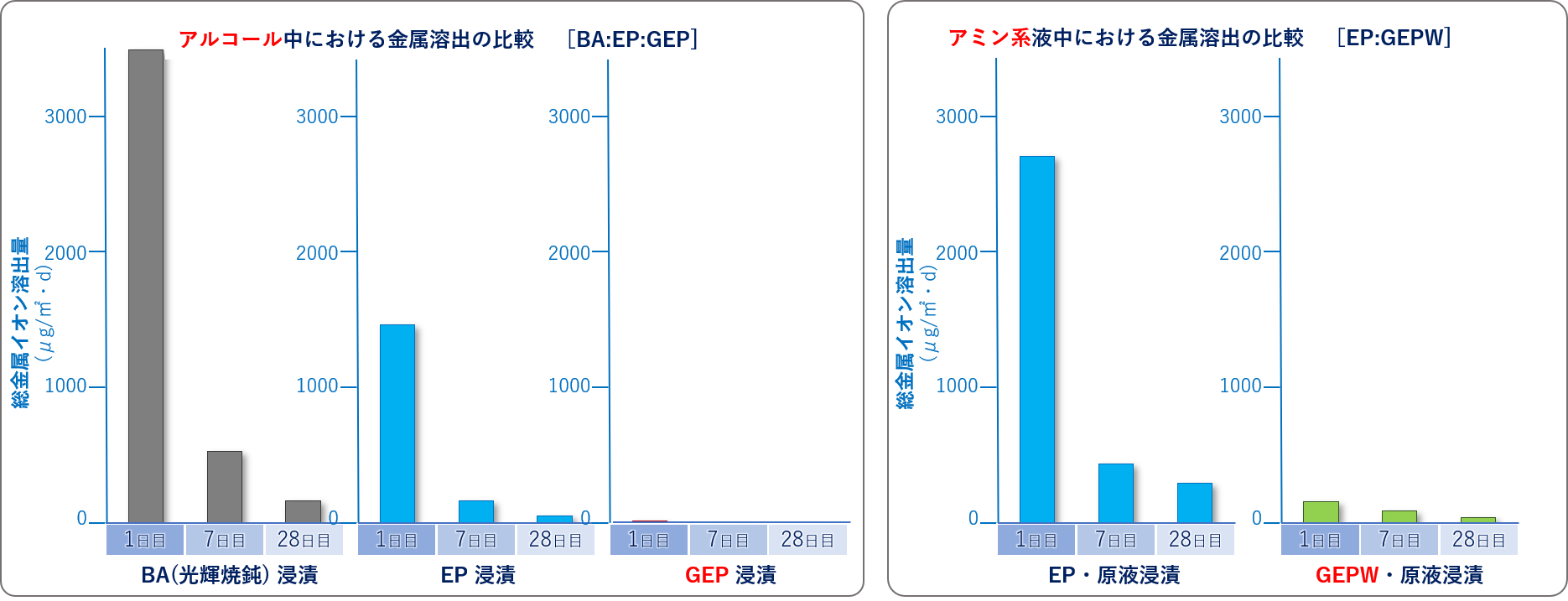
【図6-2】一般的な電解研磨(EP)とGOLD EP、GOLD EP WHITEの比較
※GEPはGOLD EPを、GEPWはGOLD EP WHITEを略しています。
一般的なフェルール付き接手を当社で電解研磨した写真を掲載します。
(1)サニタリー継手の電解研磨/GOLD EP
左側が一般的EP後の90度エルボー(奥はチーズ 2.0S)、右側がさらに熱処理を加えステンレス表面に鉄酸化皮膜を形成したGOLD EP。色の違いを除けば視覚的に大差はありませんが、GOLD EPは一般EPの約10倍の厚みを持つ強固な不動態膜が形成されています。
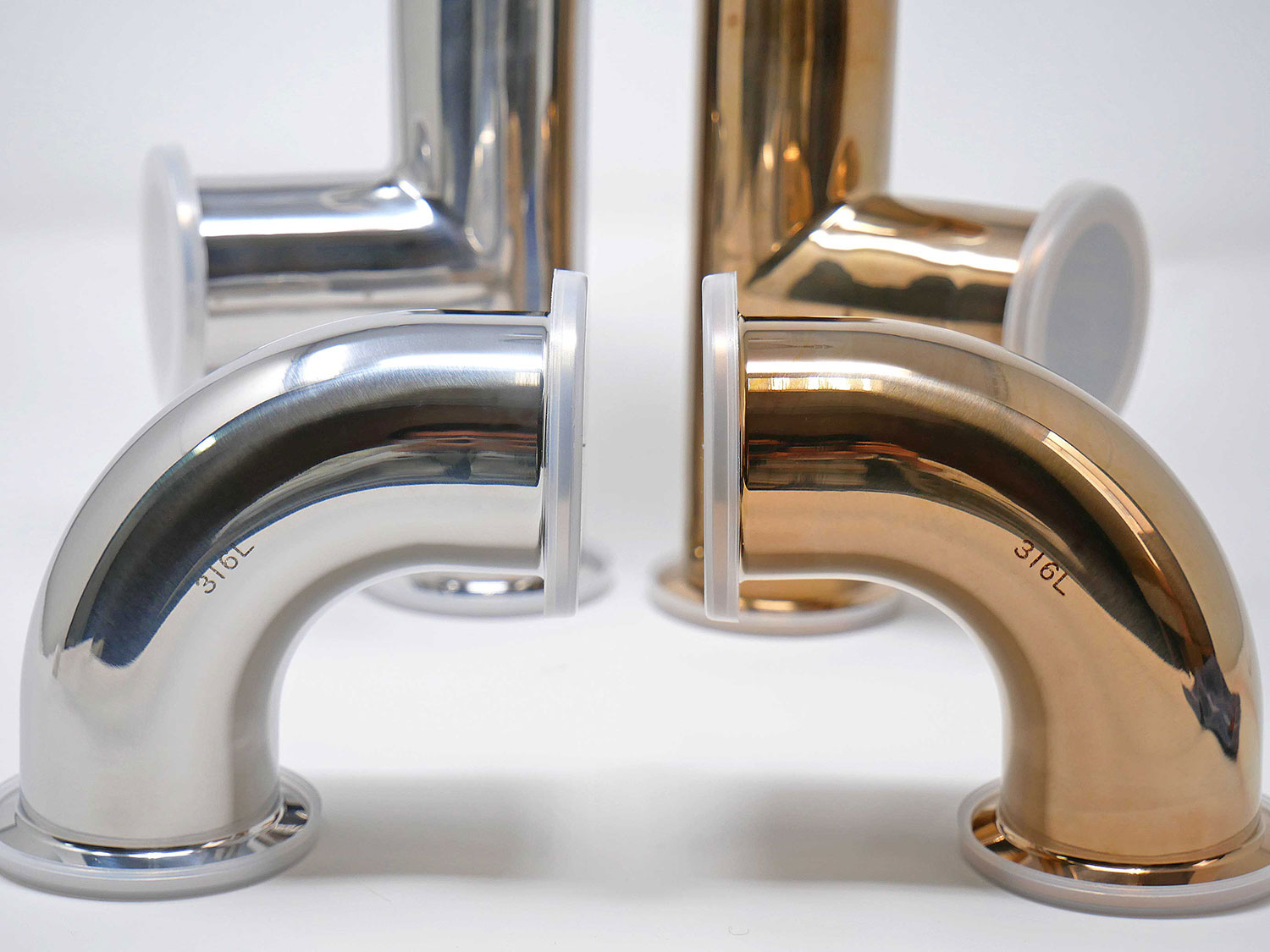
【写真6-3】一般的な電解研磨(EP)とGOLD EPを施した接手の外観比較
(2)サニタリーパイプのGOLD EP/GOLD EP WHITE サンプル
金色のパイプがGOLD EP、白色がGOLD EP WHITEです。GOLD EP WHITEは、熱処理で形成されたGOLD EPの鉄酸化皮膜を化学処理で除去したもの。除去した鉄酸化皮膜下には、厚いクロム酸化膜(一般EPの約3倍)の不動態皮膜が形成されているので、超純水や有機アミン系薬液に対して溶出が極少です。
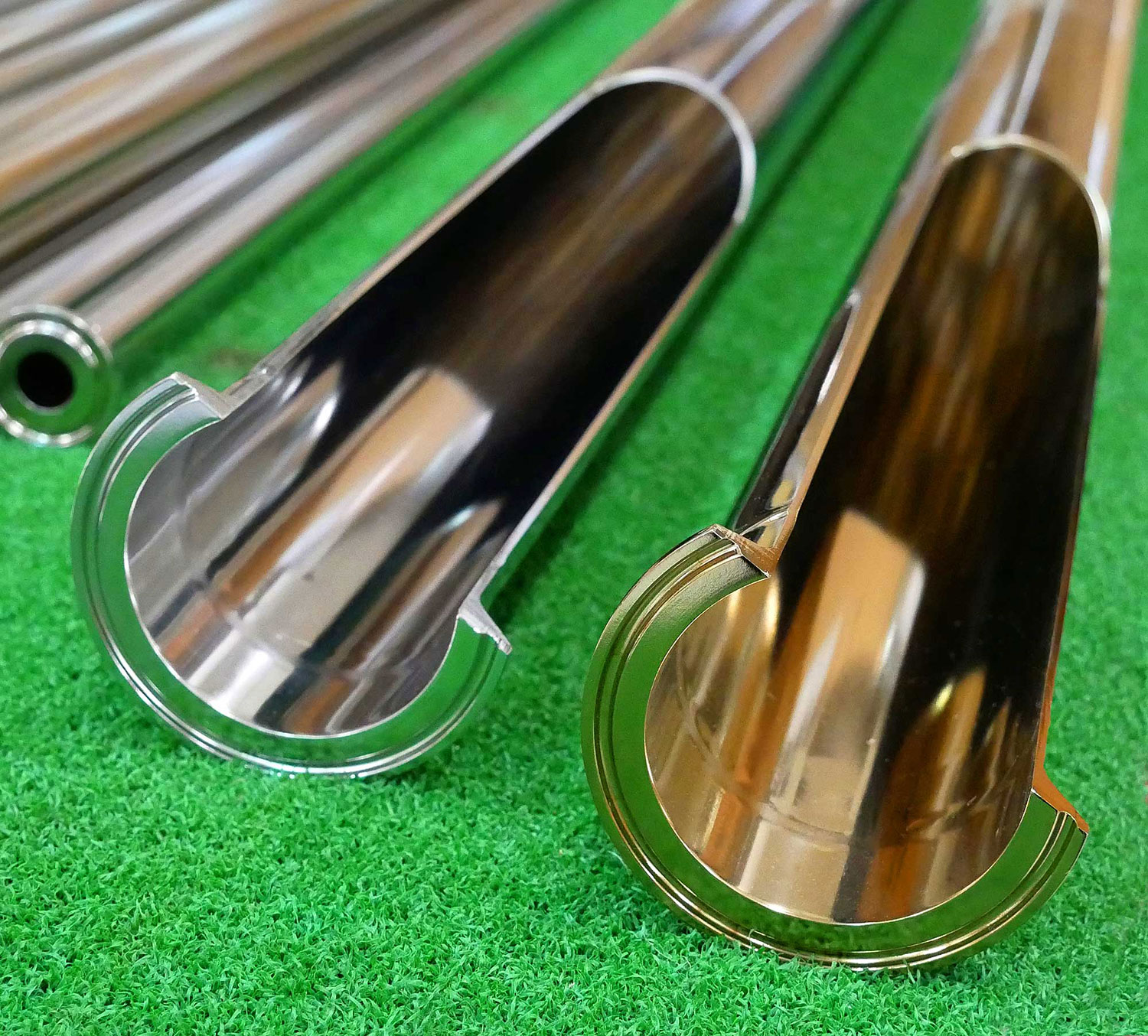
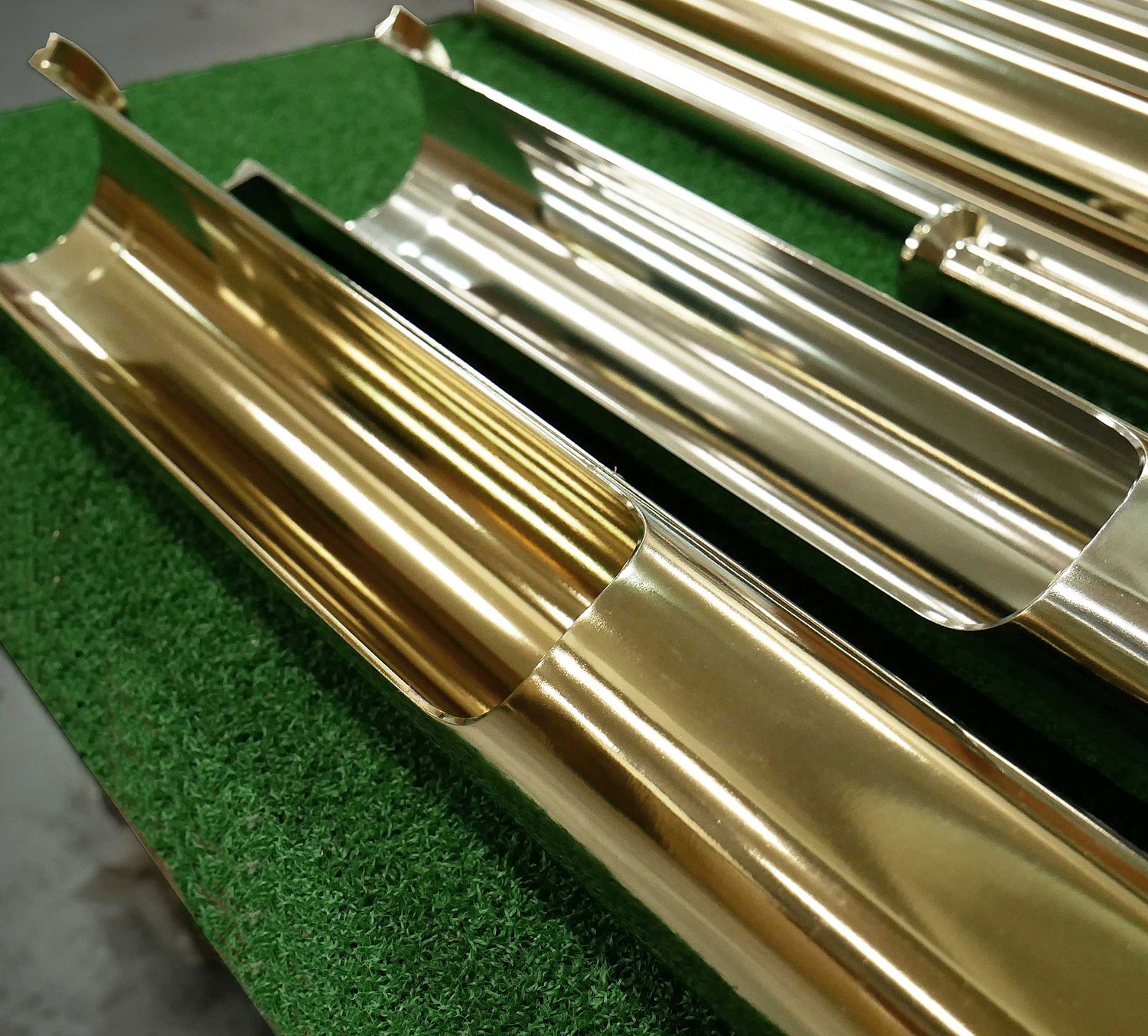
【写真6-4】 GOLD EP、GOLD EP WHITEのカットパイプサンプル
(3)ゴールドEP処理されたローター部品
生成物が通過する配管だけでなく、調味料や腐食性のある液体などの飛沫にさらされる機械類には、長期間の運用を確保するために重要部品の耐蝕対策が必要になります。
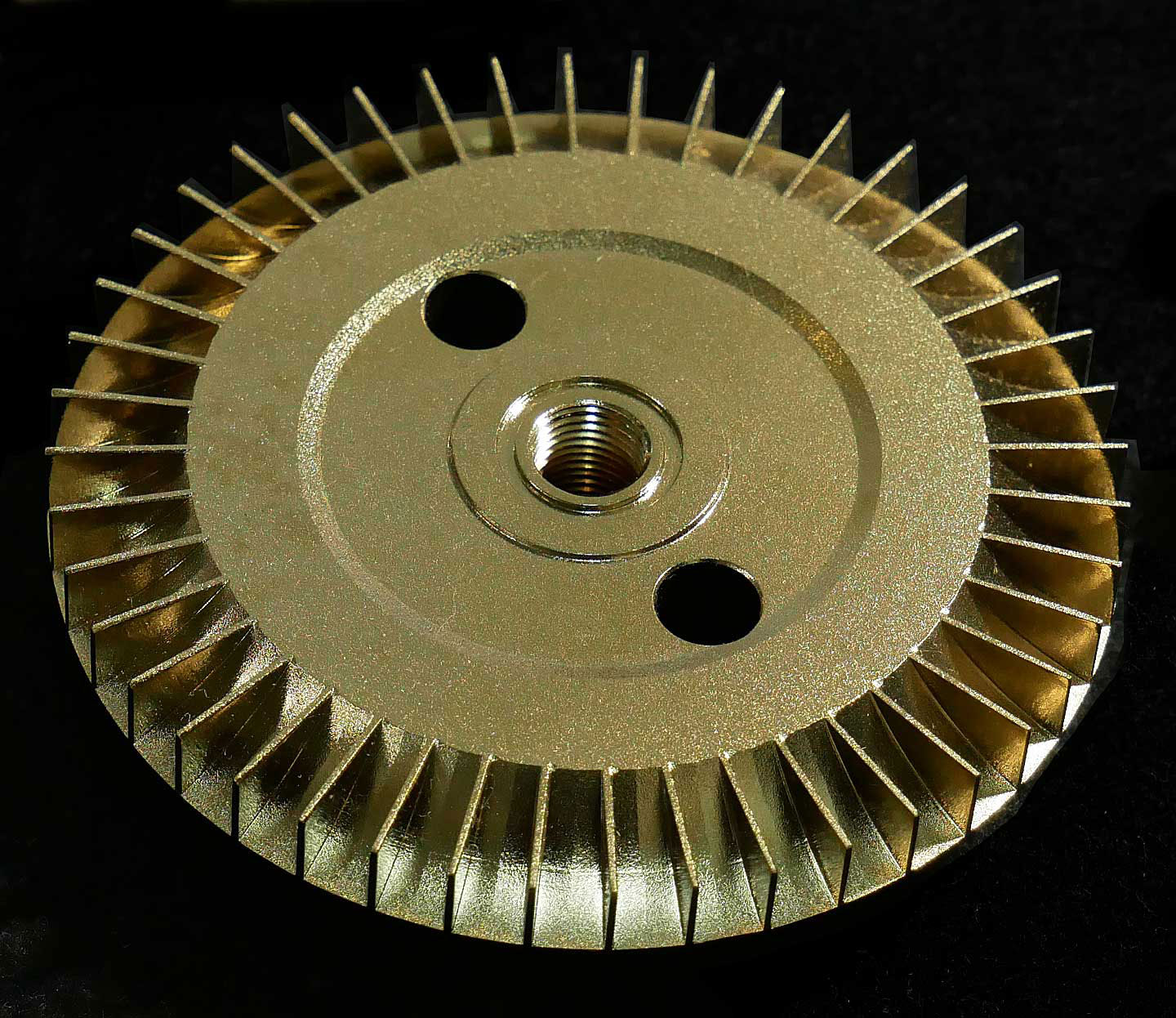
【写真6-5】一般的な電解研磨(EP)とGOLD EPを施した接手の外観比較
7.ステンレス以外の電解研磨
ベトナム現地法人VINA ASTEC CO.,LTD.では、ステンレス(Fe)に加えチタン(Ti)やアルミ(Al)などの活性金属の電解研磨を手掛け始めました。
(1)アルミニウムの電解研磨
アルミニウムの電解研磨サンプル(丸棒)です。左側がEP前、右側がEP後の写真になります。丸棒の断面と側面で仕上がりが違いますが、金属を圧延して丸棒にする時、結晶構造に方向性ができるため、断面が梨地模様になります。梨地化はステンレス丸棒のEPでも同様に現れます。
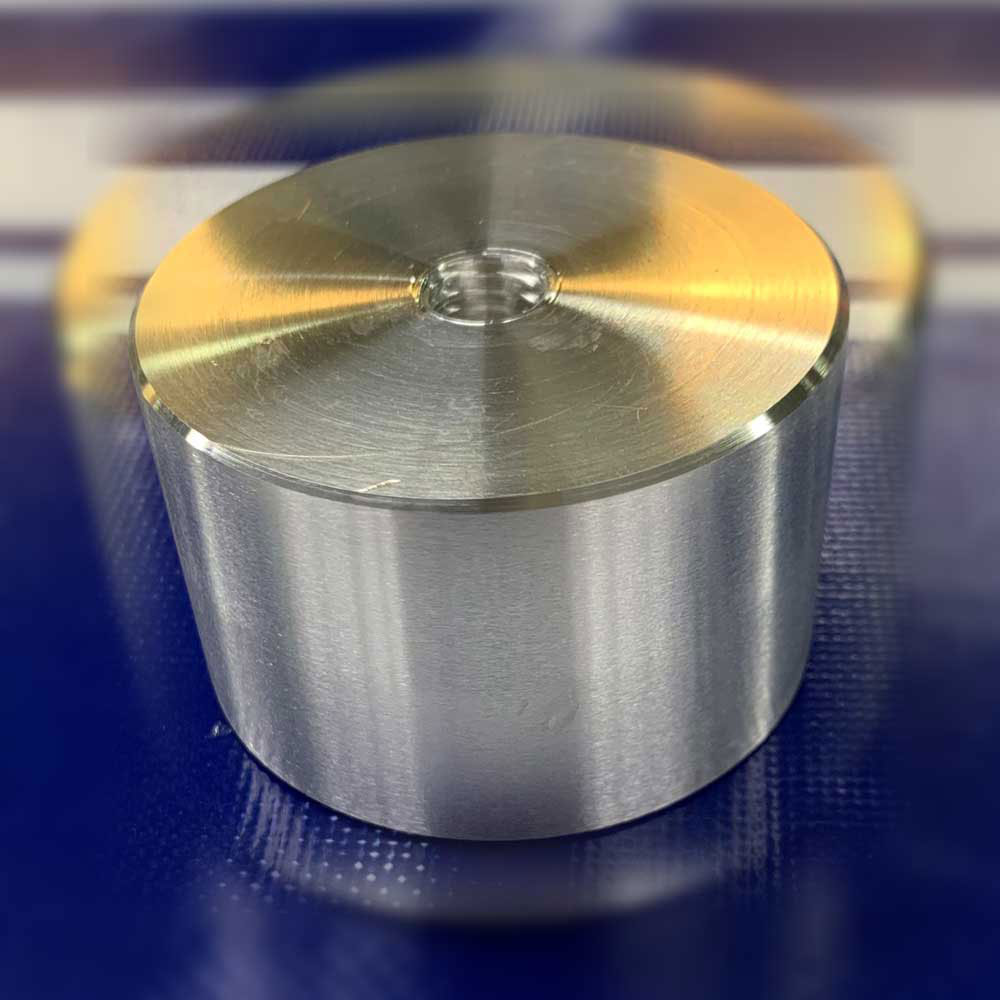
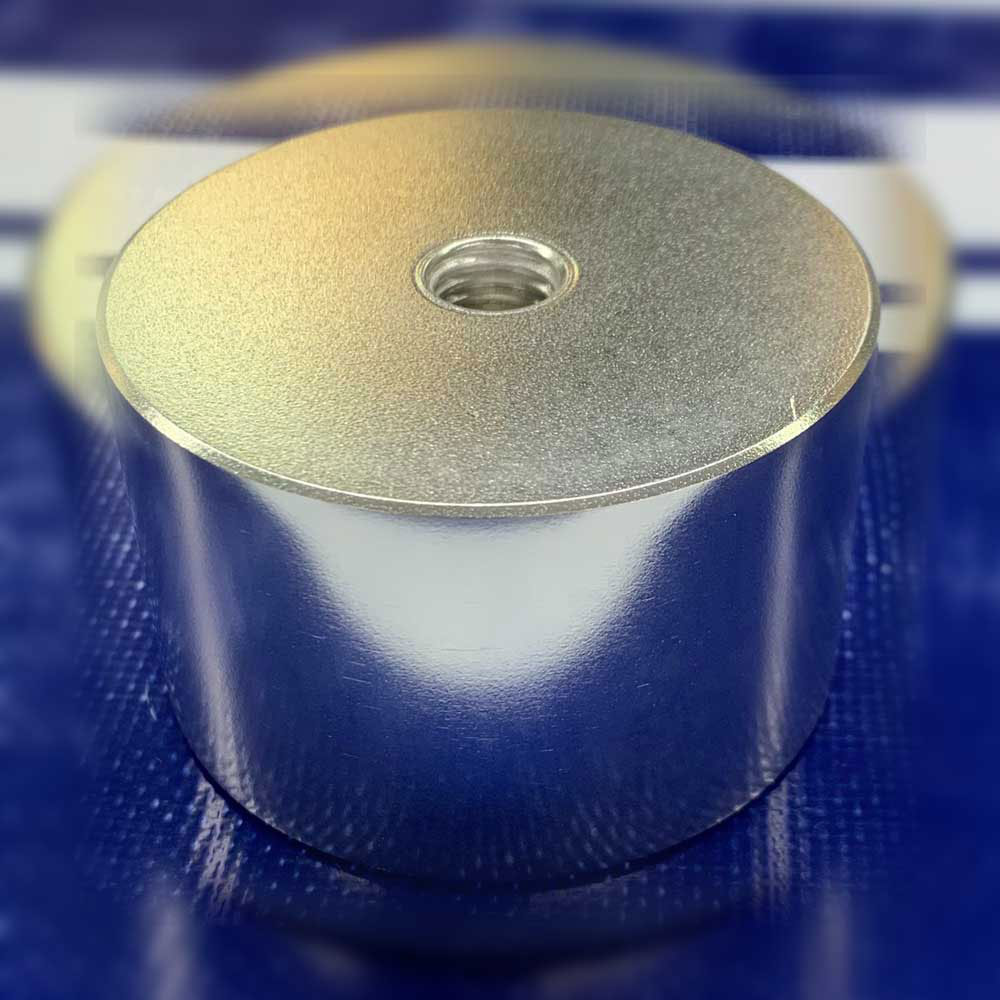
【写真7-1】 アルミニウム丸棒の電解研磨 処理前後の外観比較
(2)チタンの電解研磨
チタン部品の電解研磨サンプルです。
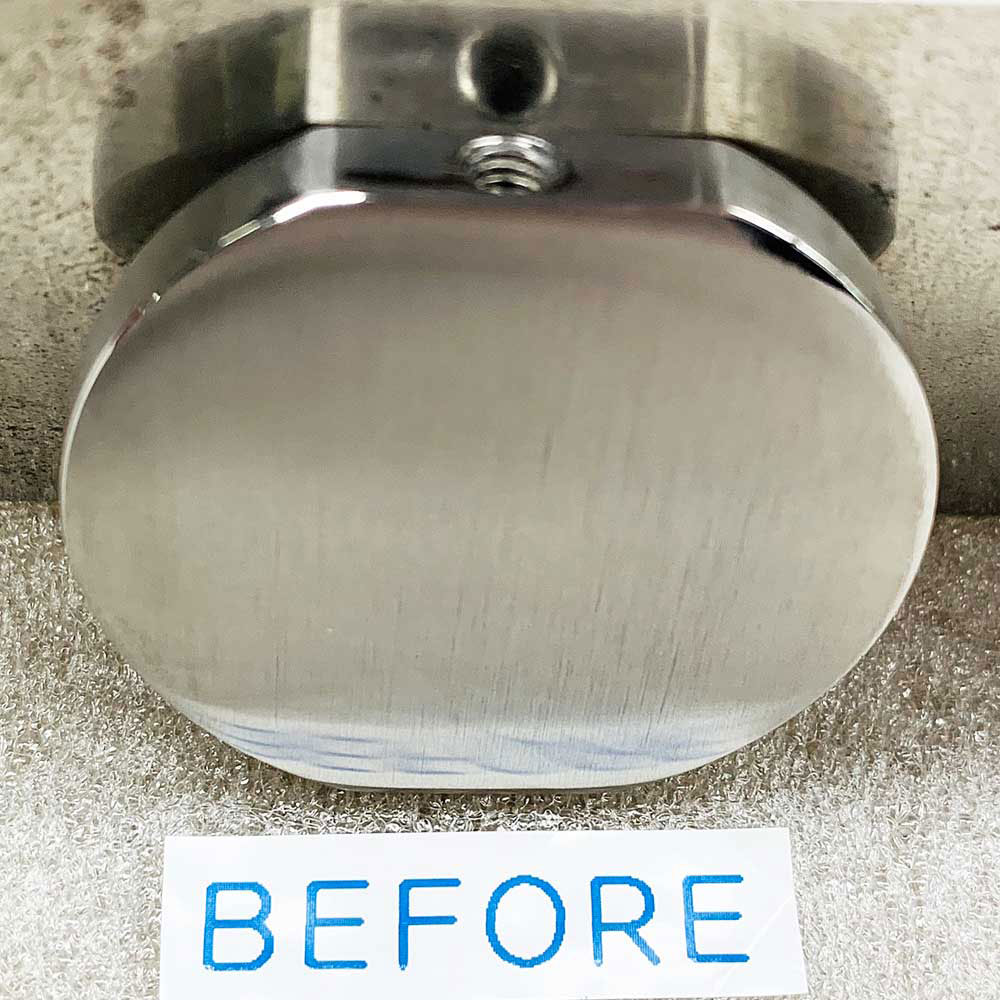
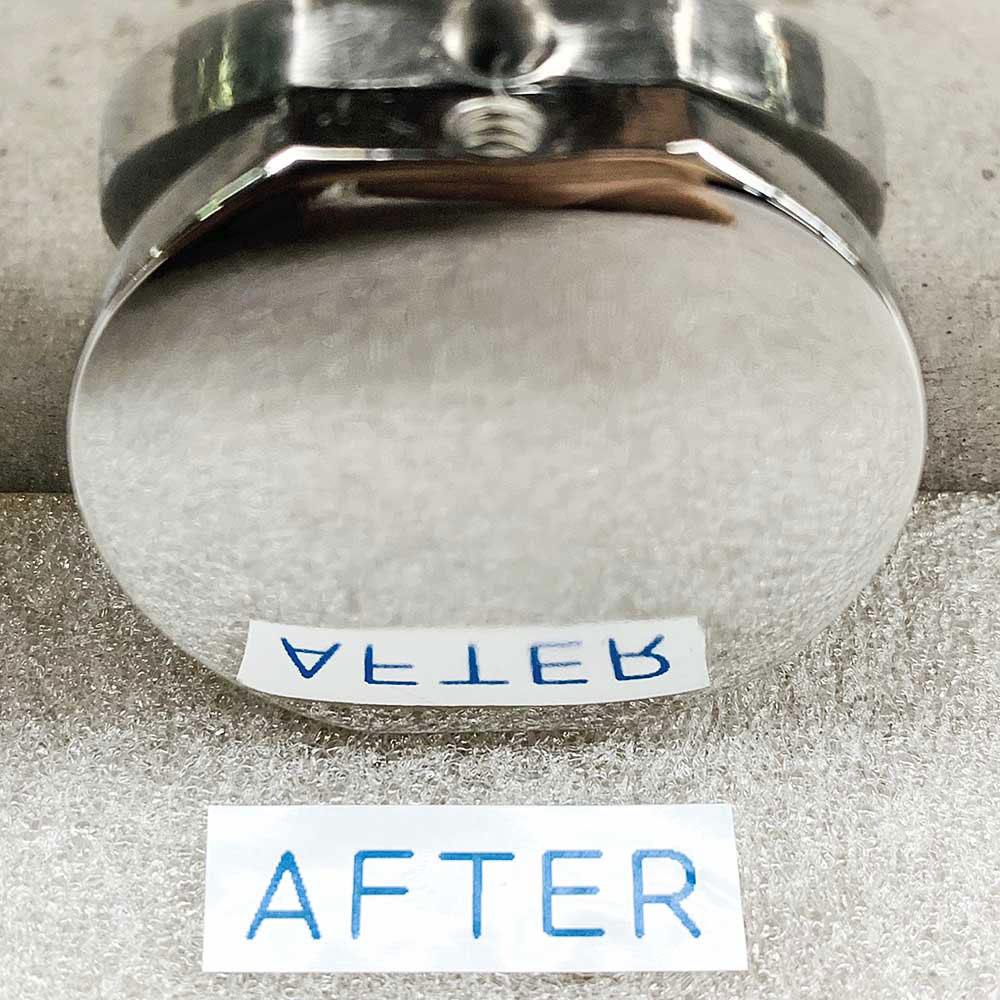
【写真7-2】 チタン部品の電解研磨 処理前後の外観比較
(3)チタンのカラーリング
チタンの陽極酸化皮膜による発色は、金属表面反射光と酸化被膜表面反射光の干渉によって生じます。形成される酸化被膜(透明)の厚みをコントロールすることによって、目的の色にカラーリングすることが可能です
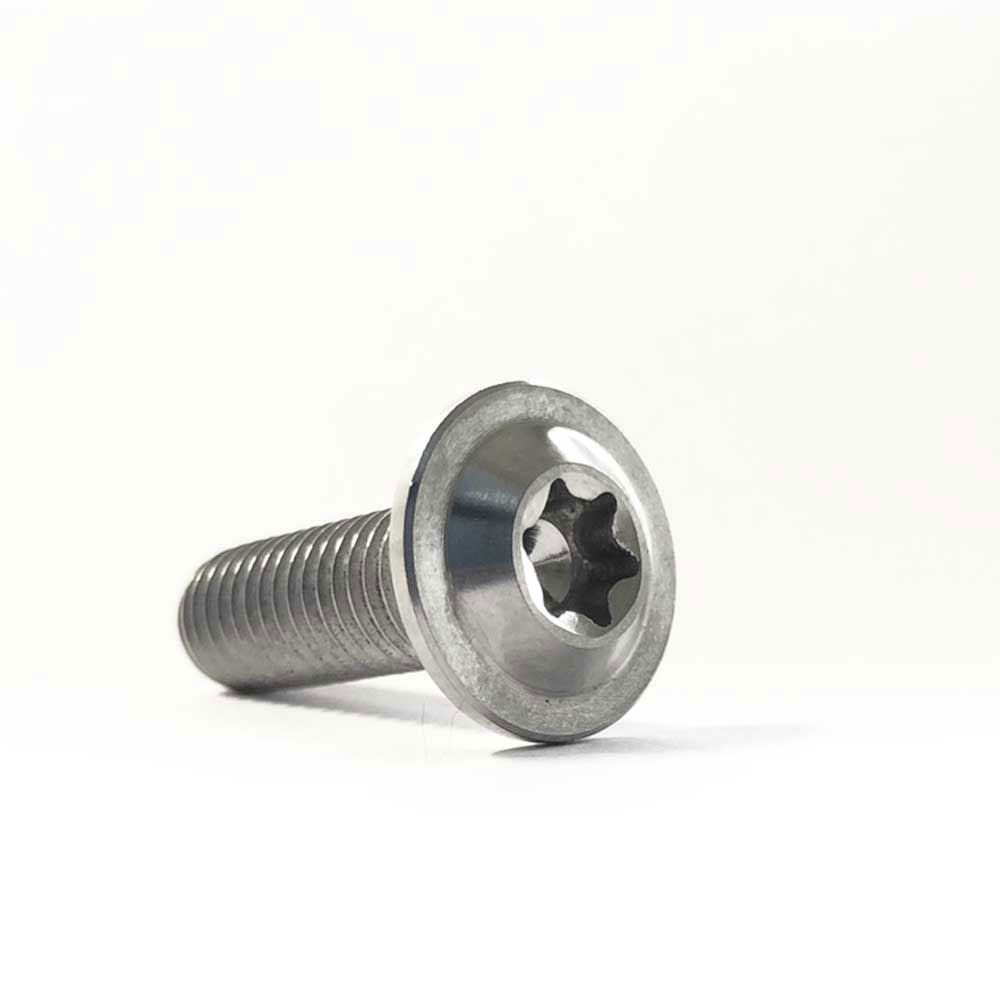
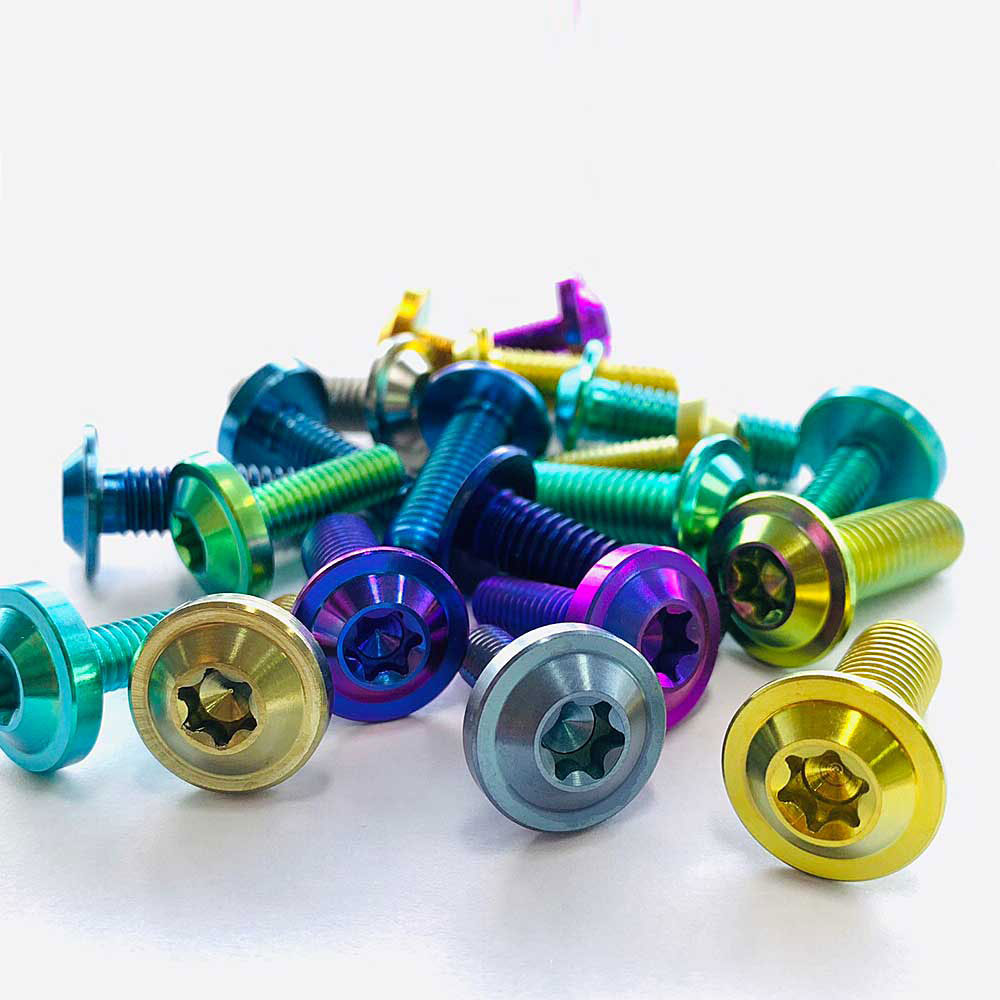
【写真7-3】 チタンねじの酸化被膜形成によるカラーリング
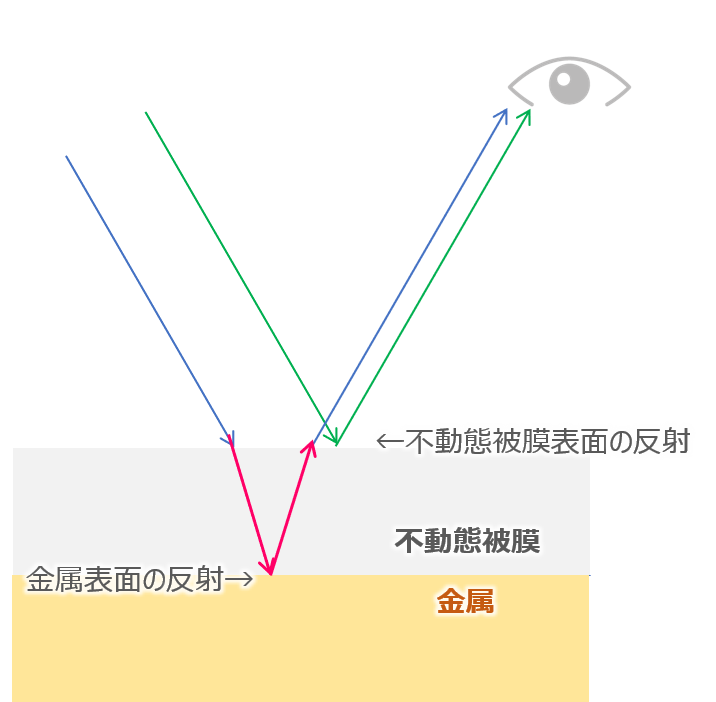
【図7-4】 反射光の干渉(位相のズレ)
チタンを覆う不動態皮膜で反射する光と、金属表面で反射する光は、同じ光源でもの不動態内を通過する距離(左図8-4赤い部分)だけ到達距離が違い、そのため位相のずれが生じます。それによって、ある波長(色)の光が弱められたり強められたりする「光の干渉」という現象が発生します。
チタンのカラーリングは塗装や染色と違い、この光の干渉を使って行いますので、金属を削ってみても見えている色の塗料が出てくるわけではありません。不動態被膜の厚みを部材全体で均一にすることで金属全体が同じ色に見え、また不動態皮膜の厚みをコントロールすることで見える色が違ってきます。
活性金属(かっせいきんぞく)
イオン化エネルギーの低い(自らの原子に電子を繋ぎ止めておく力が弱い)金属はイオン化しやすく「活性金属」と呼ばれる。鉄、アルミニウム、チタンなどは活性金属で、水または酸と反応して容易に溶解する。また、チタンやアルミニウムは鉄と比べてもたいへん活性度の強い金属で「腐食しやすい」と言える。ところが、溶出したイオンが直ちに堅固な酸化被膜(不動態皮膜)を形成するため、実用的には非常に安定した金属として活用されている。これら活性度の高い金属は、電解研磨を行う際のガス発生も活発なので注意が必要
8.最後に ~前後の工程を含め電解研磨を考える必要性
大ヒットしたスーパーマリオブラザーズが発売され、電電公社が民営化しNTTとなった1985年(昭和60年)当社は電解研磨を事業化しました。また2015年からは、ベトナム現地法人VINA ASTEC CO.,LTD.によりベトナムでも日本品質の電解研磨を行っています。
研磨対象製品の形状やサイズ
長尺のパイプ、継手、そして様々な形状の受注品に、均質で高品質な電解研磨を施すための運用や電極・治具などの製作ノウハウも豊富です。
【図8】 実際の電解研磨(EP)の様子 (YouTube当社掲載))
前後の工程を含めた表面処理品質
また当社は、機械加工から表面処理、据付工事まで一貫して担うことができ、製品がお客様の製造設備や保管施設で稼働することを常に意識してものづくりを行っています。前工程の溶接やバフ研磨のできによって電解研磨の品質が影響することも熟知し、各種洗浄や不動態皮膜をより強固に仕上げる後工程にも豊富なノウハウを持ち、お客様のご期待に沿いそして超える努力を続けています。
※本コンテンツで使用している数値、グラフ等の情報は、主に弊社「電解研磨技術資料」より引用しています。